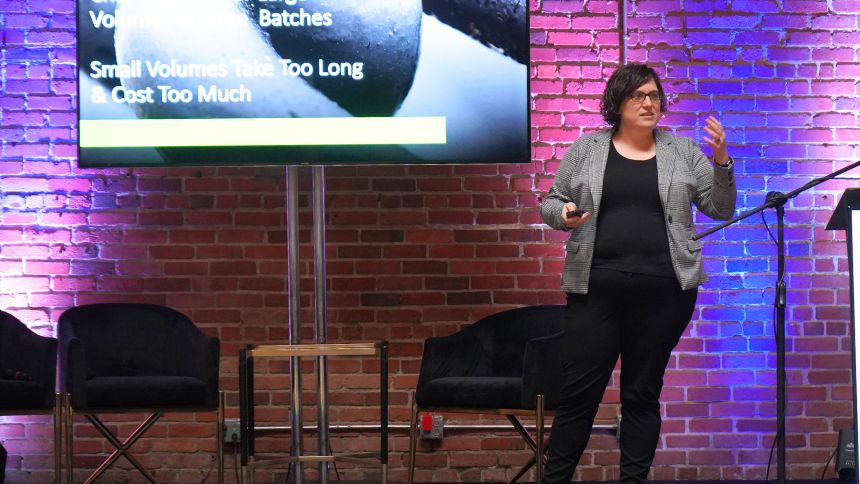
Sarah Jordan of Skuld LLC learned some lessons from an earlier start-up failure
Now, she's developed a whole new technology for additive manufacturing named AMEC and is participating in the newest cohort of "Innovation Crossroads."
Skuld LLC is not Sarah Jordan’s first start-up, so the challenges any new venture is facing are not something from which the seemingly self-assured entrepreneur shies away. No doubt that confidence comes at least in part from a failed start-up earlier in her career, the lessons she learned from that experience, and the methodical approach from a career in engineering.
As a graduate student working on her MBA at Carnegie-Mellon University during the heart of the Great Recession, Jordan and her spouse built a foundry. Things were going very well until “our biggest customer could not pay us,” she said. That brought the venture to a quick end.
While the experience was disappointing, it led Jordan in another direction, this time focused on developing a new process technology for additive manufacturing. Seven years later, she got that process named additive manufacturing evaporative casting (AMEC) working and set her sights on participating in the “Innovation Crossroads” program operated by Oak Ridge National Laboratory (ORNL).
Today, Jordan and Skuld are participants in the recently announced Cohort 2023.
AMEC joins together the capabilities of lost foam casting, which is a type of precision investment casting, and 3D printing of polymers. Compared with alternative additive manufacturing processes, it is faster, less expensive, and capable of creating larger parts with precision tolerances. It also has known microstructures for ease of part qualification.
“Our technology is 10 times faster than investment casting, 10 times more accurate than sand casting, and 90 percent cheaper than printing either,” Jordan says.
Skuld received a Small Business Innovation Research award from the Defense Logistics Agency for a project to demonstrate AMEC in aluminum and an America Makes project to develop the process for Inconel alloys.
With that level of traction, what was the attraction of joining “Innovation Crossroads”? It starts with the lab and its reputation.
“ORNL and the MDF (Manufacturing Demonstration Facility) are leaders in additive manufacturing,” Jordan said. “Working with the lab helps us sell this new process to industry.”
Explaining that Skuld has started making legacy parts that might otherwise be machined, she said it is also important from a long-term perspective to be able to go back and understand the fundamental research that underpins AMEC.
“We can make parts,” Jordan explains, adding that the company has produced parts ranging in weight from a quarter of a pound to 85 pounds. “We want to get it right the first time rather than through trial and error.”
As a participant in “Innovation Crossroads,” she also hopes to make the process even faster than it is today and easier to do. “We’ve made castings in 11 hours without tooling, but we believe we can make them even faster.”
Finally, Skuld is also beginning to build equipment for others who want to adopt the AMEC process. The Lightning Metal 16 is planned for launch in October.
Jordan earned two engineering degrees from The Ohio State University and is working on her Ph.D. at Worcester Polytechnic Institute. She also has a diverse industrial background.
Describing Skuld as a bootstrapped company, Jordan says she is considering raising a round of between $500,000 and $1 million.
Like what you've read?
Forward to a friend!