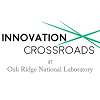
PART 3: Using father’s tools as youngster sparked Justin Nussbaum’s interests
(EDITOR’S NOTE: This is the third article in a five-part series spotlighting the work of the second cohort of start-ups comprising Oak Ridge National Laboratory’s “Innovation Crossroads” initiative. They arrived in the area in May to begin their two-year effort to further advance their early stage energy-focused companies.)
By Tom Ballard, Chief Alliance Officer, PYA
One characteristic of many young entrepreneurs we have met and interviewed since launching teknovation.biz in early 2012 is the influence that their parents had on their pursuits. That’s certainly the case with Justin Nussbaum who is part of the second cohort of Oak Ridge National Laboratory’s (ORNL) “Innovation Crossroads” initiative.
The Founder and Chief Executive Officer of Ascend Manufacturing told us that his father had a lot of tools that were available to the young son as he grew-up in Clearwater, FL. “I enjoyed using them and, over time, they slowly became mine,” Nussbaum says. “I liked to take things apart. If I wanted something, I just built it.”
That curiosity led him to the University of South Florida where, as a volunteer at the school’s Micro-Integration Lab, Nussbaum was exposed to 3D printing. His interest in 3D printing began with the repair of a Fab@Home, one of the first commercially available hobby-level 3D printers. Nussbaum then used the printer to conduct research for his master’s degree and made his first invention disclosure for that work.
And, as they say, “game on” as his career path, at least for now, has been established. Ascend Manufacturing is developing an additive manufacturing system, called Large Area Projection Sintering (LAPS), that offers many advantages over new and traditional technologies. With LAPS, components can be economically created with increased production rates, reduced peak processing temperatures, and extended exposure times, enabling the processing of a broader range of materials while also providing superior mechanical properties.
“Our 3D printers are capable of making single components or can be used for the mass production of parts with superior performance, exotic materials and with integrated quality control and assurance,” Nussbaum writes on his LinkedIn page.
The recent USF graduate, with a doctorate in mechanical engineering, has been working on improving 3D printing technology for more than a decade. In fact, he filed a provisional patent five years ago for an origami approach to 3D-printing that allowed a component to be quickly produced in a flat orientation and later folded into a high strength 3D structure.
Later, based on input from his advisor, Nussbaum started using powdered material, an oven and an entire layer based fusing process that employs a projector to literally project a high-intensity image onto the powdered material, fusing it in the shape of the projected image.
“That was Gen 0 . . . proving the concept of using a projector to melt high strength engineering thermoplastics,” he said. Think of Gen 0 as the proof of concept system. Gen 1 involved making parts through the new 3D projection process. “It was very slow,” Nussbaum said, taking over 8 hours in some cases to make a single one inch long part.
While very time consuming, the parts were stronger and more ductile than other 3D-printed parts, but the curious Ph.D. candidate wanted an answer to the question, “Why are we getting better properties?” He has a partial answer.
“We’ve been able to narrow down what has caused this.” Nussbaum answers. “We believe it’s due to the melting and recrystallization process, but we don’t know much about the crystal structures which are forming.” Finding the answer to that question is a key reason that Ascend Manufacturing applied for the “Innovation Crossroads” program.
“We need to understand the science . . . what is happening and why,” Nussbaum says. Getting the answer will allow him to optimize the process to make the strongest parts possible and go forward with a commercialization plan.
Where does he see early opportunities?
“One area I mention most is the mass manufacturing market . . . from thousands to tens of thousands of parts,” Nussbaum explains, adding that “injection molding and machining have limitations. We want to bridge the gap between low volume and high volume production.”
His ultimate goal is to make and sell the 3D printers as well as provide services to those who buy them. To achieve his goal, Nussbaum is focused only on the manufacturing process research at ORNL. He is developing the machines separately on his own time in his garage.
In terms of being part of Cohort 2, he describes ORNL as “a pretty amazing environment. Here, you ask a question, they give you the answer, or connect you with someone who can. It’s the perfect environment. I feel extremely lucky to be here.”
NEXT: Eonix.
Like what you've read?
Forward to a friend!