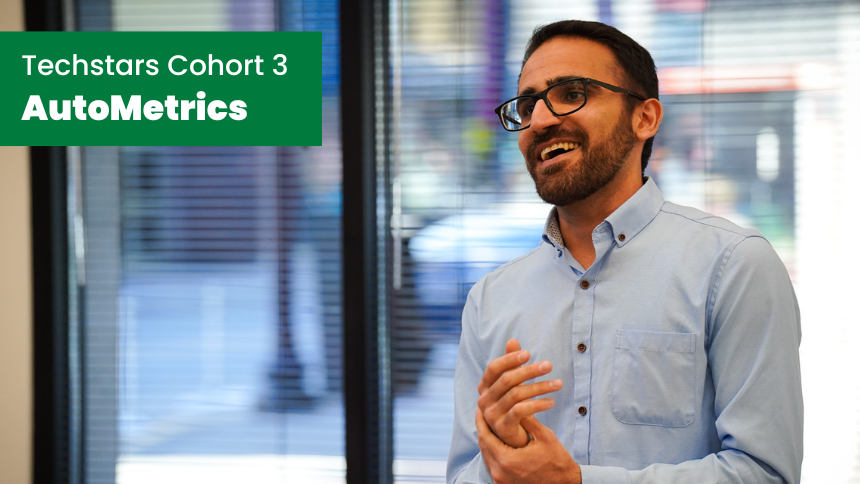
AutoMetrics is building the machine brain for industrial automation
The start-up's Inspection 4.0 system monitors welding operation quality in real time via process-level quality indicators using advanced Machine Learning software.
Mike Mohseni is totally focused on quality and quality monitoring for manufacturers.
A little more than four years ago, he turned that passion into a new start-up named AutoMetrics that is committed to enhancing manufacturing quality by building the machine brain for industrial automation.
Today, Mohseni and the company are participating in Cohort 3 of the “Techstars Industries of the Future Accelerator” currently underway in Knoxville. Demo Day is set for 4 to 8 p.m. EDT June 6 at Regas Square, 333 West Depot Avenue, and the public is invited. To register, click here.
He grew-up in what Mohseni says was a business-oriented family in Iran. After graduation in 2013 from the Sharif University of Technology with a Bachelor of Applied Science degree in Materials Science and Engineering, he moved to Vancouver, Canada where he continued his education, earning a Master of Science in Mechanical Engineering and Ph.D. in Composites Manufacturing, both from the University of British Columbia.
In addition to being a Research Assistant and later Graduate Teaching Assistant at the University, he also worked as a Simulation and Machine Learning Engineer for Applus+, a worldwide leader in the testing, inspection, and certification sector, and was a Research Assistant at the Composites Research Network that is part of the University of British Columbia.
“Our research team and I closely collaborated with Boeing (in) Everett,” Mohseni told us, explaining that he saw the significant cost and complexity of ensuring product quality in large-scale production lines.
Today, he wants to combine his education, experience as a researcher, and AutoMetrics to focus on the next generation of intelligent manufacturing.
The company’s currently offered product is named Inspection 4.0. It monitors welding operation quality in real-time via process-level quality indicators using advanced Machine Learning software.
Mohseni says that the technology can detect potentially detrimental deviations, just like an experienced welder’s eye would do. It is fully automated, finding the welding defects in real-time, and alerting the user through a remote monitoring unit.
“Our Virtual Weld Master accelerates troubleshooting by directing users to the root-cause of the deviations,” Mohseni adds.
As a result, the system reduces significant risks to the user:
- Profit loss due to reworks by avoiding defects vs. finding them after the process;
- Delays and backlogs from downtime by addressing issues in real-time; and
- Defective product and reliability loss by monitoring quality of each and every part.
Mohseni says he applied to be a participant in the “Techstars Industries of the Future Accelerator” for several reasons.
“As a first-time founder, there’s a bit of a learning curve,” he says. “I also saw the need for investment dollars to spur AutoMetrics’ growth,” specifically citing funding for four or five pilot projects with original equipment manufacturers and Tier 1 suppliers.
Mohseni also saw value in linking with the three partners, particularly the University of Tennessee which he said would be a “good resource for talent.”
Like what you've read?
Forward to a friend!