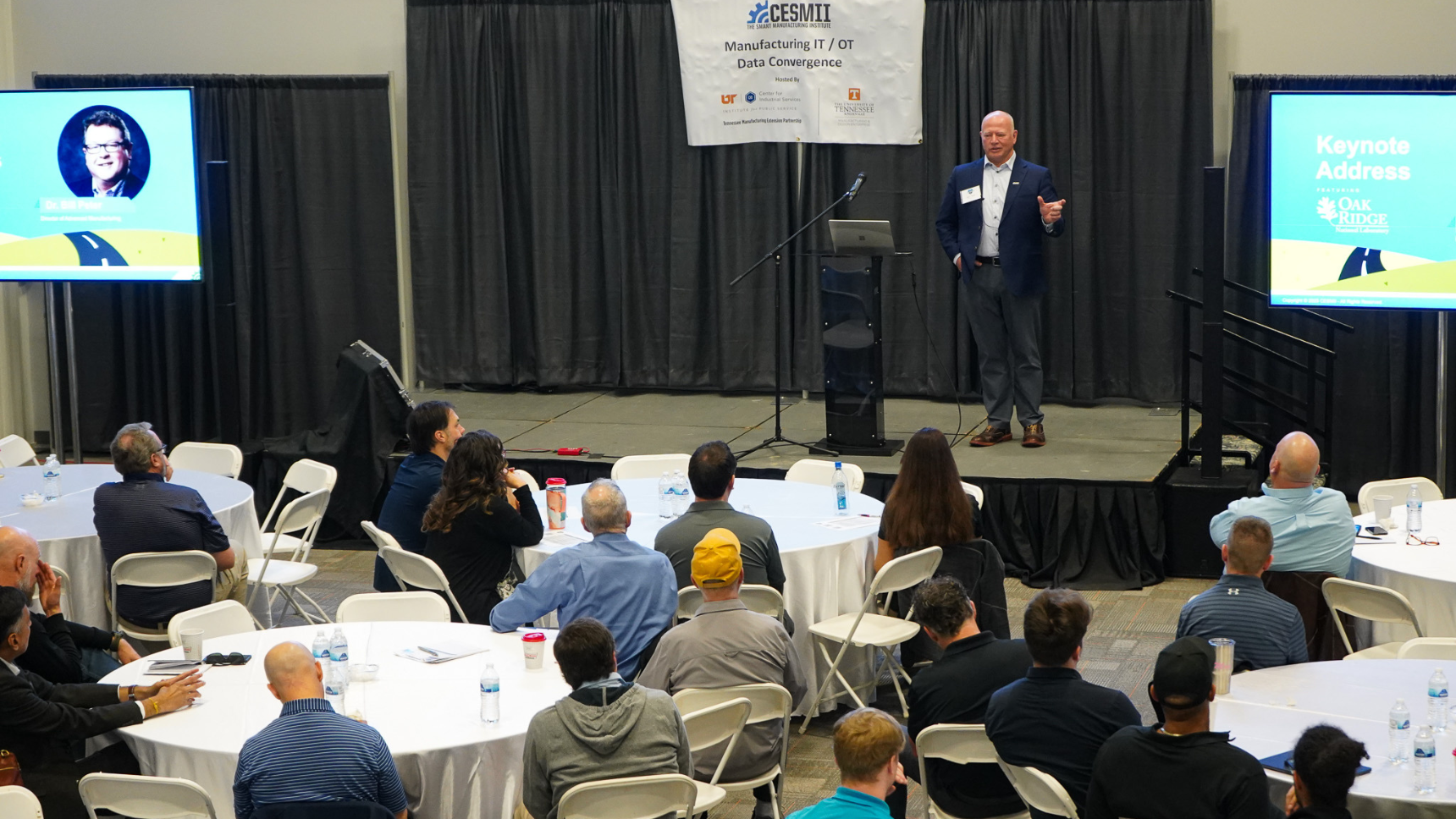
Industrial Revolution 4.0 is here, and CESMII is helping local manufacturers level up to the challenge
This nationwide event series brings CESMII representatives to cities across the country, connecting with small and medium-sized manufacturers (SMMs), Manufacturing Extension Partnerships (MEPs), and the broader manufacturing ecosystem.
Nine out of ten manufacturers across the country don’t have a smart manufacturing strategy. Smart manufacturing, which involves utilizing advanced emerging technologies to enhance the efficiency of traditional manufacturing processes, is key to fostering a more agile and productive industrial base. After adapting to smart manufacturing, companies experience greater levels of efficiency, lean manufacturing, and cost savings
However, in an industry that functions at such a rapid pace, the burden of implementation time can be a deterrent. That’s why CESMII (The Smart Manufacturing Institute) is helping educate and empower manufacturers in Tennessee to take the leap. They hosted the “Smart Manufacturing Roadshow” on Wednesday, attracting a little under a hundred people out to the Institute for Advanced Materials & Manufacturing in Hardin Valley.
“We have a roadmap and framework to assess manufacturing facilities and professionals to where they are, and how we can accelerate their business through emerging technologies,” John Dyck, the Chief Executive Officer (CEO) of CESMII said.
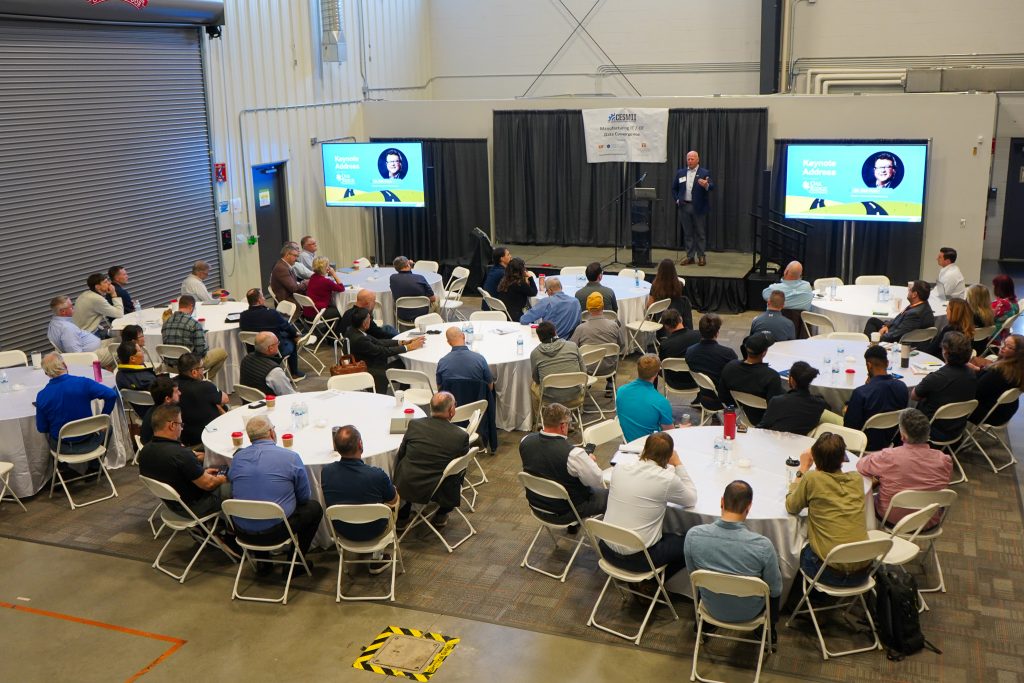
He talked about the emergence of the “Industrial Revolution 4.0,” and how what has been idealized for a long time is coming to fruition. The transformative shift in manufacturing is primarily driven by advanced digital technologies such as cyber-physical systems, the Internet of Things (IoT), big data, artificial intelligence (AI), and cloud computing. With so many directions to turn – where is the best place to start?
“Digitizing your plant floor operations will increase production levels anywhere from 30 to 50 percent,” Dyck said. By installing cameras or data readers on various machines it can help detect deficiencies and defects.
Dyck explained it like a bucket full of water. As manufacturers continue to patch the holes (pain points) they will retain more product and have greater margins.
“The first step is collecting data so you know where the holes are at,” Dyck said.
Throughout the rest of the day-long event attendees heard from a number of speakers in the advanced manufacturing sector.
Notably, Dr. Bill Peter, the Director of Advanced Manufacturing at Oak Ridge National Laboratory (ORNL) provided a keynote on several key innovations ORNL is testing at the Manufacturing Demonstration Facility (MDF).
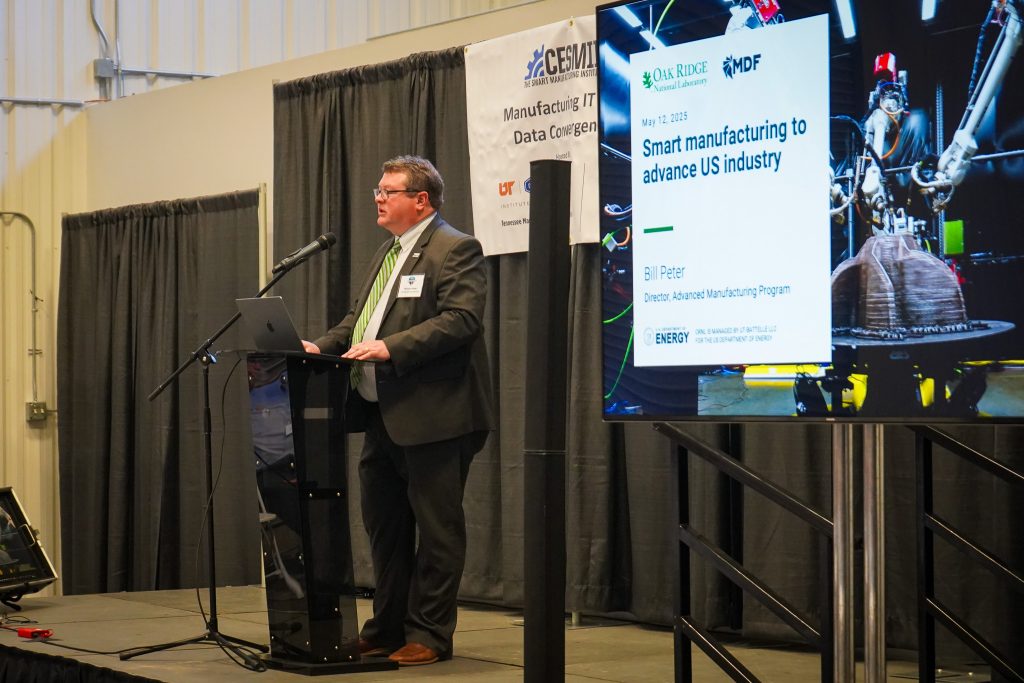
The MDF is a fully operational facility with cameras and artificial intelligence built into or onto every machine. The whole operation is collecting data on design, optimization, and efficiency.
Additionally, MDF attracts about six thousand outside visitors per year who are interested in the implementation of the smart manufacturing model.
“ORNL also has an open-sourced modeling software for manufacturers that we can engage companies on,” Peter said. If any parties are interested visit the MDF website.
Other event speakers included Dr. Vasileios Maroulas from the University of Tennessee, Knoxville (UTK), who spoke on AI TechX. Teknovation featured the initiative on Thursday (see story here). Plus a number of breakout session leaders: Sudhi Bangalore – FullBore, John Louka – CESMII, Ryan Cahalane – Axiom Systems, Dr. Sai Swaminathan – UTK, Jeremy Nathan – JN Computer Training.
Like what you've read?
Forward to a friend!