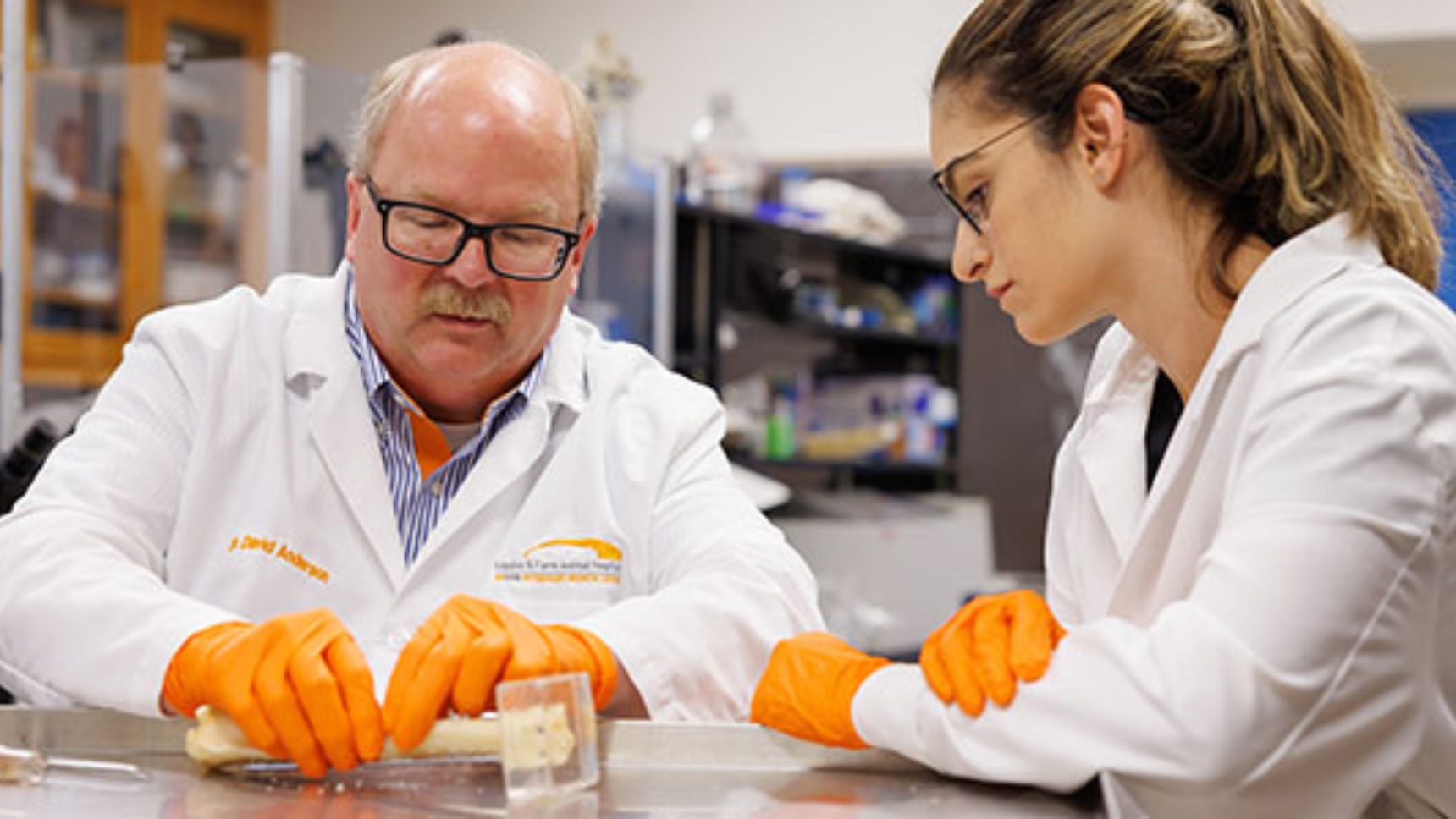
Regenerative innovations are underway in the medical space at UT, Knoxville
Two researchers started a company, NuShores BioSciences to commercialize the cutting-edge research.
At the University of Tennessee, Knoxville (UTK) College of Veterinary Medicine, David Anderson, the Associate Dean for Research at the college, alongside a research team, is exploring innovative technology aimed at healing bones without permanent metal plates and screws.
“The traditional approach to repairing a bone gap is putting implants in the body that help restore form and function, but that process leaves you with this hardware permanently,” said Anderson. “We have been developing degradable technologies that heal the body but don’t remain in the body forever.”
Anderson said that a body can naturally recover from a certain level of bone loss.
For over 14 years, he has partnered with Alexandru Biris, Director of the Center for Integrative Nanotechnology Sciences at the University of Arkansas at Little Rock, to advance this bone regeneration technology.
Their collaboration led to the creation of highly porous polymeric scaffolds, which bridge bone gaps and guide surrounding bone tissue to fill these spaces.
“Like the scaffolds you see construction workers using on the side of a building, these scaffolds are mostly space,” Anderson said. “They are 3D structures designed for the bone tissue to grow into the spaces in the scaffold. The scaffold allows the tissue to know where to go.”
The two researchers co-founded NuShores BioSciences LLC to bring this transformative technology to the market, which Anderson believes could redefine aspects of medical treatment.
He envisions a time when bones, joints, and scaffolds are 3D-printed to custom specifications for each patient. At UT Knoxville, researchers are already paving the way for this future, including Rigoberto Advincula, the UT-Oak Ridge National Laboratory (ORNL) Governor’s Chair for Advanced and Nanostructured Materials in UTK’s Tickle College of Engineering.
“We are using 3D printing to prepare regenerative implants that are degradable—that are harmless for the body to metabolize,” said Advincula.
Advincula’s team, located in UT’s Institute for Advanced Materials and Manufacturing, goes beyond creating shapes for bones and scaffolds. They’re also designing and 3D printing tendons that can connect bone to muscle while testing their flexibility and strength.
“When we design tendons, they need to have the flexibility of tendons and the durability of bones,” Advincula explained.
Read more from the UTK press release.
Like what you've read?
Forward to a friend!