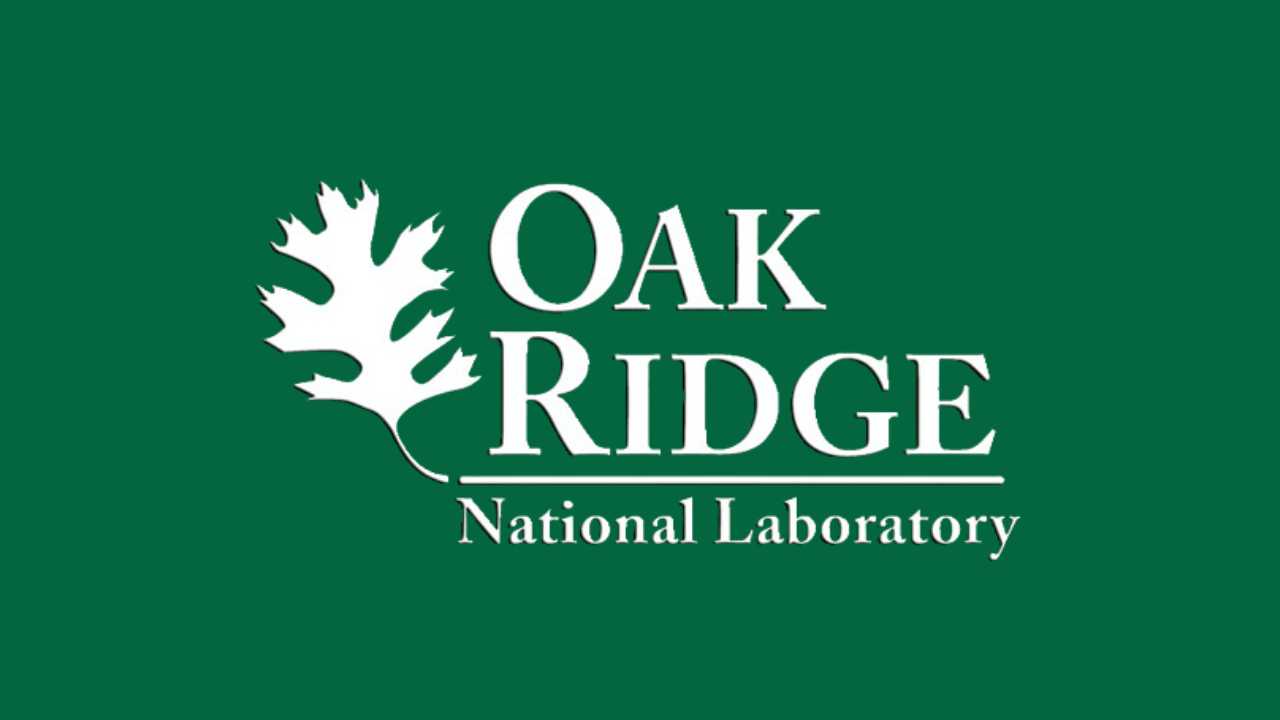
ORNL researchers bringing new life to very large metal parts manufacturing
It's a very viable alternative to casting and forging known as powder metallurgy-hot isostatic pressing (PM-HIP).
Researchers at Oak Ridge National Laboratory (ORNL) are using advanced manufacturing techniques to revitalize the domestic production of very large metal parts that weigh at least 10,000 pounds each and are necessary for a variety of industries, including clean energy.
Across sectors spanning aerospace, defense, nuclear, oil, gas, renewables, construction and more, sourcing these large-scale components is an increasingly urgent challenge. This need is felt acutely in the U.S., where traditional manufacturing techniques like casting and forging have declined and moved overseas — resulting in supply-chain shortages.
Today, ORNL researchers are advancing an increasingly viable alternative to casting and forging known as powder metallurgy-hot isostatic pressing (PM-HIP). Their research has the potential to bring large-component manufacturing back to the U.S.
Senior Research Scientists Jason Mayeur and Soumya Nag are innovating to push PM-HIP far beyond its decades-old origins with the addition of process improvements — including the use of 3D-printing methods like wire-arc additive manufacturing and hybrid (additive and subtractive) manufacturing, as well as in-situ monitoring and advanced computational modeling. These techniques can create PM-HIP molds faster and more accurately. In turn, PM-HIP is made not only more precise and effective, but also more affordable, and more viable for American manufacturing.
“PM-HIP is a vital pathway for diversifying the supply chain for producing large-scale metal parts that are becoming more difficult to source via conventional means,” Mayeur said. “The technology is of particular interest to the nuclear and hydroelectric industrial sectors, as well as the Department of Defense.”
In contrast with traditional casting and forging techniques, the PM-HIP manufacturing process involves fabricating pre-formed, hollow molds for each large-scale component and filling them with metal powder. Once the 3D-printed mold, also known as a “can” or “capsule,” receives an initial seal, any gas remaining inside is pumped out. Then, a more permanent, hermetic seal is applied.
At this point, the capsule is heated and pressurized in prescribed cycles within a hot isostatic press, or what is essentially a pressurized furnace. Without melting, these cycles facilitate the consolidation of the metal powder into the required shape, in a process exchange of heat and pressure known as solid-state bonding. When bonding is complete, acid leaching or machining is used to remove the exterior can, revealing the intended part.
Like what you've read?
Forward to a friend!