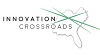
Hicham Ghossein reutilizing scrap and recycled chopped fibers for non-woven mats
(EDITOR’S NOTE: This is another in a series of seven articles spotlighting the start-ups that comprise Cohort 3 of Oak Ridge National Laboratory’s “Innovation Crossroads” program.)
Reutilizing scrap and recycled chopped fibers and turning them into long fiber non-woven mats is the focus of Hicham Ghossein, Founder and Chief Executive Officer of Endeavor Composites Inc., one of the participants in Cohort 3 of Oak Ridge National Laboratory’s (ORNL) “Innovation Crossroads” (IC) program.
Ghossein, born in the Middle Eastern country of Lebanon, came to the U.S. 11 years ago to work on the first of two Master’s degrees at the University of Alabama at Birmingham. When his major professor – Dr. Uday Vaidya – moved to the University of Tennessee (UT), Knoxville to accept a position as a UT/ORNL Governor’s Chair in Advanced Composites Manufacturing and later added the role of Chief Technology Officer, Institute for Advanced Composites and Manufacturing Innovation (IACMI), Ghossein moved here to work on his doctorate in mechanical engineering.
“It was not much of an orthodox Pd.D.,” he said. “We had a lot of industry engagement, designing prototypes. It exposed me to a lot of industry needs.”
Much of that work occurred in the Fibers and Composites Manufacturing Facility on White Avenue on the UT, Knoxville campus. And, because of the opportunities that he saw, Ghossein based his doctorate on new ways to make non-woven carbon fiber.
One might describe it as the less glamorous side of carbon fiber. These are applications that would be under the hood of a vehicle rather than the hood itself of a high-end Lamborghini. Potential areas include parts with complex shapes such as door panels and cabin heat shields. They do not need the much finer finish that a car hood must have.
“We have created a solution for recyclers, a product for industry, and a way to handle waste,” Ghossein says, noting the use of something that had to be disposed of to now produce a new product.
One key component of the technology that has been developed a technology to produce nonwoven textile using long chopped carbon fiber. Developed at lab scale, the machine provides a consistent product that not only works with carbon fiber, but all known fibers and even allows a mixing of different fibers.
“UT (Research Foundation) has filed for a patent,” Ghossein says, adding that his company just executed an 18-month license option in late December in a defined field of use.
During the two-year IC fellowship, he expects to focus on scaling-up the machine from bench to pilot line scale as well as making more connections with industry. Ghossein grades the solution at a TRL 3 scale and wants to get it to at least TRL 6 before the program ends. TRL stands for Technology Readiness Level, and achieving his goal would mean the next step – TRL 7 – would involve demonstration of an actual system prototype in an operational environment.
“We want to be sure Murphy doesn’t have any tricks up his sleeve,” Ghossein says in explaining the great value of the IC program.
Assuming Murphy does not, he sees a very bright future for the company. “There are not too many non-woven companies in existence, and millions of pounds of the material are going to be needed over the next 40 to 50 years,” Ghossein says. “The potential is endless with this material.”
The Founder also has other big goals including becoming a Tier 1 supplier to the automotive industry. “Every car has at least 5,000 parts,” Ghossein says. “My goal is to supply at least 1,000 of them.”
Like what you've read?
Forward to a friend!