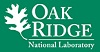
ORNL home to new battery manufacturing R&D facility
(EDITOR’S NOTE: The following release was provided by Oak Ridge National Laboratory.)
OAK RIDGE, Tenn., June 25, 2012 — Future automotive batteries could cost less and pack more power because of a new manufacturing research and development facility at Oak Ridge National Laboratory.
The $3 million Department of Energy facility allows for collaboration with industry and other national labs while protecting intellectual property of industrial partners. The laboratory is attracting battery manufacturers, chemical and materials suppliers, system integrators and original equipment manufacturers.
“We’re able to integrate advanced material components into a complete battery, analyze how it perform and better understand how to improve it,” said Claus Daniel, deputy director of ORNL’s Sustainable Transportation Programs. “With this capability, we can isolate and evaluate a material or process and quantify any advantage that each would provide.”
Through the nation’s largest open access battery manufacturing R&D facility, American businesses could gain a competitive advantage in the global market.
“R&D facilities such as these are critical in the development of advanced battery technology that is more affordable and more durable than today’s batteries,” said Patrick Davis, program manager of DOE’s Vehicle Technologies Program.
The facility features two chambers totaling 1,400 square feet of space along with state-of-the-art battery manufacturing equipment. One chamber allows researchers to maintain relative humidity levels of between 0.5 and 15 percent. This room houses equipment that allows for mixing of various slurries, stabilization, coating and drying.
The second chamber provides a dew point of minus-40 degrees Celsius, which translates to a relative humidity of 0.5 percent. This is necessary to prevent moisture from entering and degrading battery cells. In this chamber, electrodes, cathodes and anodes are assembled automatically into pouches that are filled with a precise amount of electrolyte. The pouches are then trimmed and sealed through a heating and vacuum process.
Researchers can make batteries with up to 7 ampere-hours capacity, a size that provides good demonstration capability but requires less material, reducing the burden on smaller companies that lack large-scale production capacity.
Working with others, Daniel looks forward to many successes.
“ORNL’s combination of equipment and expertise allows collaborators to develop and optimize processes, manufacturing schemes, perform diagnostics and maximize yield,” Daniel said. “Working with industry, we’re advancing the field and moving closer to creating a battery that will allow automobiles to travel longer distances on a single charge.”
ORNL has a dozen contracts with eight battery-related companies in their quest to compete in a global marketplace.
Funding for this project was provided by DOE’s Office of Energy Efficiency and Renewable Energy. UT-Battelle manages ORNL for the Office of Science. The Office of Science is the single largest supporter of basic research in the physical sciences in the United States and is working to address some of the most pressing challenges of our time. For more information, please visit http://science.energy.gov/
Like what you've read?
Forward to a friend!