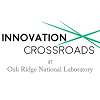
PART 5: TCPoly developing thermally-conducted materials to improve heat dissipation
(EDITOR’S NOTE: This is the final article in a five-part series spotlighting the work of the second cohort of start-ups comprising Oak Ridge National Laboratory’s “Innovation Crossroads” initiative. They arrived in the area in May to begin their two-year effort to further advance their early stage energy-focuses companies.)
By Tom Ballard, Chief Alliance Officer, PYA
“We decided we wanted to pursue a company and make something real out of our research,” Matt Smith, Co-Founder and Chief Executive Officer of TCPoly Inc., told us.
The other part of the “we” equation is Co-Founder Thomas Bougher, a fellow classmate in the doctoral program at Georgia Institute of Technology. “We were doing our doctorates together and shared a small closet office with no windows for four years,” Smith said.
In October 2016, they launched TCPoly to develop a new class of high thermal conductivity plastic composite materials designed to improve heat dissipation, allowing for metal replacement and light-weighting, cost and component reductions, and improved performance and reliability. The materials also exhibit the unique ability to be 3D-printed, allowing thermal engineers to rapidly and inexpensively prototype multi-functional thermal solutions and enabling the design of heat transfer products that cannot be manufactured using traditional methods.
Today, Smith is participating in the second cohort of Oak Ridge National Laboratory’s (ORNL) “Innovation Crossroads” initiative, while Bougher remains at the start-up’s home office in Atlanta. Both are engaged full-time in the new venture.
“We have complementary skills,” Smith says. His doctorate is in materials science and engineering, while Bougher’s is in mechanical engineering. They started the company with six 3D printers and a couple of polymer extruders housed in, you guessed it, Bougher’s garage.
“We were initially trying to make a plastic that would conduct heat and make it into a form to sell in traditional manufacturing like injection molding,” Smith explained. “We realized there was a lot of pain, cost and time involved in injection molding prototyping.”
So, they decided to focus on reformulating their materials in a way that they could be 3D-printed.
“We made our initial 3D printing filaments less than a year ago and have been working constantly to improve them,” Smith said. “We knew we were onto something based on forums we found with others searching for this type of material. That provided early confidence.”
With ORNL’s reputation in additive manufacturing including the world class Manufacturing Demonstration Facility in Hardin Valley, it was only natural that the TCPoly team would find the opportunity to participate in “Innovation Crossroads” very attractive.
“We want to make materials that can be printed on commercially available printers,” Smith explained. To do so, he is tweaking the formulations and understanding how each of them performs.
“Our hope is that by focusing of functional materials, we can produce higher value products,” he says. That, in turn, will make mass production through 3D printing more feasible.
An early target market is high power LED lighting where there are large metal heat sinks. TCPoly believes its thermally-conducted material can be used to replace the metal sinks and remove the heat. In addition to performing that function, the start-up’s material is corrosion resistant, lighter weight and electrically insulating.
“We need to enter the market at the simplest level,” Smith explains. As such, TCPoly is initially focusing on products with simple geometries that can be printed fast and with high throughput. Their long-term business plan calls for the company to supply the materials and design support to customers who would then do their own manufacturing.
Like what you've read?
Forward to a friend!