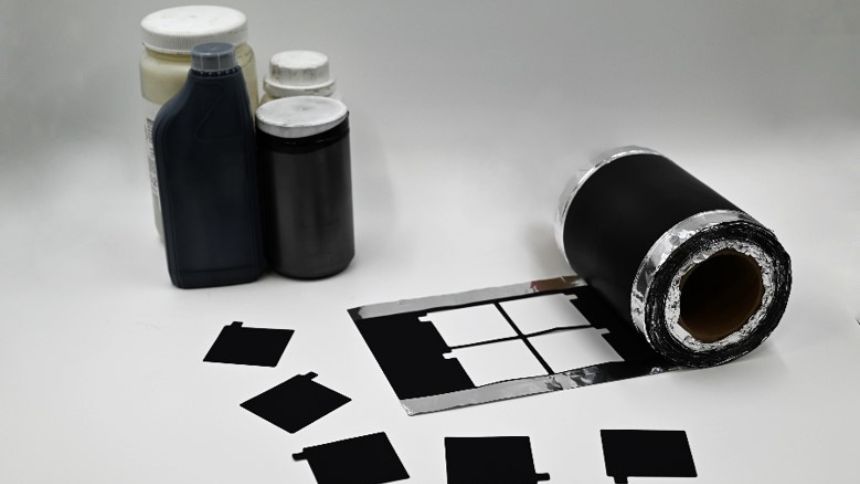
Ateios Systems providing sample packs of its new technology at The Battery Show
The company's has partnered with ORNL to develop the platform technology called RaiCure that uses energy-curable, PFA-free, polymers to replace traditional electrode manufacturing methods.
A company that was part of the 2022 cohort of the “Innovation Crossroads” program at Oak Ridge National Laboratory (ORNL) will be offering sample packs of its new RaiCureTM technology to device developers during The Battery Show North America that began October 7 in Detroit.
That company is Ateios Systems, a manufacturer of battery components that recently announced the release of its RaiCureTM High-Voltage Lithium Cobalt Oxide (HV LCO) electrodes, enabling the world’s first perfluoroalkoxy-free (PFA), rechargeable LCO battery. LCO batteries comprise the most significant portion (33 percent) of the $85 billion battery market as the critical chemistry that powers consumer electronics such as wearables, cellphones, and many more.

Founded by Rajan Kumar, who also serves as the start-up’s Chief Executive Officer (CEO), the company is housed at The Battery Innovation Center in Newberry, IN and has partnered with ORNL to develop the platform technology called RaiCureTM that uses energy-curable, PFA-free, polymers to replace traditional electrode manufacturing methods. Instead of using solvents and heat to induce a transition from a resin to a dry film, the RaiCureTM uses a shower of electrons to chemically polymerize and crosslink small molecules (i.e., monomers, oligomers, and low molecular weight polymers) into high molecular weight polymers.
Why is that important? There are several reasons.
For starters, lithium-ion batteries are critical in achieving the environmental goals set by COP28, calling for a nearly 14-fold increase in battery production to power electric vehicles and grid storage. Due to this increase in demand, the battery market is expected to grow from $85 billion in 2024 to more than $470 billion by 2033. While many companies have been able to boost energy density and drive costs down to make them competitive for fossil fuel-powered devices, Kumar believes the real challenge lies in the manufacturing.
“It took nearly 50 years for global battery production to surpass one TWh in 2023, and we need to build the next nine TWh in the next six years,” he said. “To supply nearly 10 TWh of batteries, we need to build enough electrodes to cover the area of Massachusetts, and the current process is just too expensive, slow, and negative for the environment to achieve it by 2030.”
Kumar told us that the traditional electrode manufacturing method involves slurry-based processes using polyvinylidene difluoride (PVDF) binder dissolved in the toxic solvent, N-Methyl-2-pyrrolidone (NMP). A single production line in a gigafactory using the solvent process will consume more than $8 million worth of natural gas to remove these solvents. It also requires a large equipment footprint of 80 meters of ovens, has low production speeds, and mandatory solvent recovery systems that can cost more than $20 million.
RaiCureTM process technology, developed in conjunction with researchers at ORNL, enables up to a 94 percent reduction in processing cost; reducing the energy consumption from ~151 MJ per kWh of battery manufactured for NMP/PVDF processing to ~27 MJ per kWh, an 82 percent reduction. This also translates into a much lower associated greenhouse gas emission in manufacturing, reducing from ~93 pounds CO2 per kWh to ~17 pounds CO2 per kWh. If this technology produced the 2,000 GWh of lithium-ion batteries expected in 2024, it could reduce CO2 emissions by 38 million tons, accounting for 0.1 percent of the global energy-related CO2 emission in 2022 (36.8 Gt).
In addition to the operational and cost savings, the Ateios team demonstrated notable performance benefits. Batteries with energy-curable polymers demonstrated an eight percent improved battery life compared with PVDF-polymers, over 1000 cycles and at high voltages. The stability of the polymer to extend to high voltages enables the end user to extend the energy out of the battery. The energy-curable polymers demonstrated a nearly 3X improvement in adhesion, critical to achieving high yields and stable performance over the battery’s lifetime. Ateios was able to achieve these key milestones with less than $3 million raised at the time of writing.
In addition, the suppliers of these energy-curable monomers have certified that their polymers are PFA-free, enabling the batteries to be made entirely free of forever chemicals, marking an overall positive environmental impact.

“Having spent the past four years testing both incumbent and emerging solutions, it is tough to see anything be as versatile as the RaiCureTM technology,” said Kevin Barry, Ateios Systems’ Vice President of Engineering. “What is great about what we are doing is it is scalable. It is not a fantasy. We can be cost-competitive in a global marketplace.”
Les Alexander, CEO of The Battery Innovation Center where Ateios Systems is located, reiterated many of those points emphasized by Kumar and Barry. Established in 2013, the Center has worked with about 500 customers at its 18,000-square-foot facility in Newberry and has an additional 6,000-square-foot building under construction in Indianapolis.
On several occasions, he described the RaiCureTM technology as a “game changer for battery manufacturing,” noting everything from the elimination of toxic materials to the cost reductions.
“It’s a good model for technology development,” Alexander said.
Like what you've read?
Forward to a friend!